Rollers for Energy Efficiency
1st December 2022
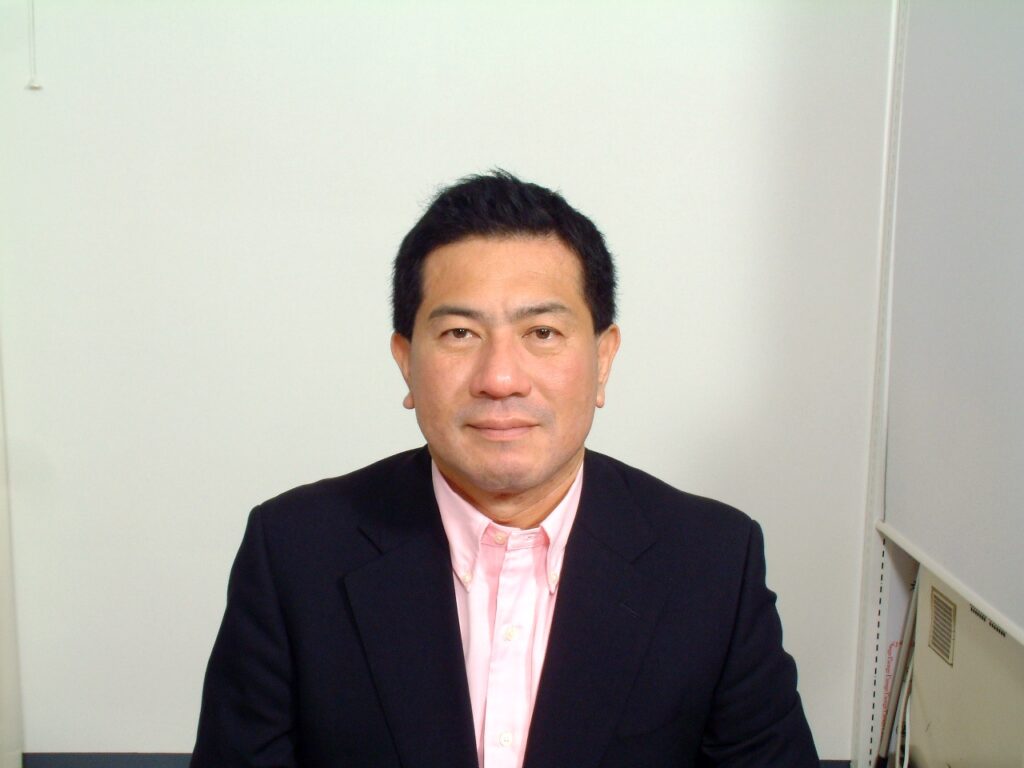
A warehouse optimised for maximum efficiency isn’t always optimised for minimal energy use, but a veteran rollers manufacturer has a solution.
Founded in 1946 as a specialist maker of motors for fans and washing machines, Itoh Denki became a pioneer in the industry when its founder invented the Motorised Drive Roller (MDR). By putting the motor and gearbox inside the body of the roller, the company was launched into the intralogistics industry. US Post chose to adopt this new roller technology, and then Itoh Denki’s future as a major player was sealed when it introduced brushless 24V technology to conveyor systems. This meant considerably higher safety levels, as the rollers neither snarled body parts nor did they impart potentially life-threatening electric shocks to unwary operatives – unlike the brutal 400V AC motor-driven rollers they replaced.
“The rollers have just enough torque that, if you want, you can stop one roller with your hand,” says Tatsuya Akashi, president of Itoh Denki’s European operations. “But its biggest advantage is that you can make each one-metre-long conveyor independent. In the past, an entire 200m conveyor would be powered to move just one small part, which was a waste of energy. Now we can move only the section of the conveyor which the part is on, saving up to 60% in electric energy.”
Describing MDR deployment as “new technology”, Mr Akashi says half of the existing conveyors in the world are old technology. “Right now, they are being replaced, so our growth potential is huge.” Ecommerce is the sector most suited to benefit, as ambitious short lead times can only be met thanks to the widespread use of MDRs in large DCs.
Wider rollers
But whilst the majority of sales are to businesses handling small parts (up to 50kg) in plastic totes or carton boxes, Itoh Denki also produces a roller with a wider diameter, making it attractive to the automotive sector as it can convey parts weighing up to 500kg as well as pallets weighing up to a tonne.
Mr Akashi believes the company’s claimed 60% energy saving is the highest in the sector, fuelling its growth. “Only in Europe, we were slightly behind our largest competitor in market share,” he says. “In the past five years, we’re doing four times more sales than before, so I think we are now in equal number one position.”
Offering modules featuring 90° right-angle transfer and free angle diverters, Itoh Denki evangelises a diverter-centric approach to sorting. “I have nothing against the crossbelt sorter,” says Mr Akashi, “but we’re talking about a new way of sorting. Today, there are still a lot of old theory believers from the crossbelt era who are stuck to just one way of layout thinking, which can be extremely costly. Take ASRS technology. You replace pickers walking and climbing stairs with a stacker crane weighing sometimes a few tonnes. It can run several hundred metres and acceleration is extremely fast, but the energy used just to take one box or one pallet from the end of the warehouse is very high. I would say that, if you do a circle and use our technology to have a conveyor with lifter storage, you don’t need to run such a big train. So if everybody thinks about energy, we can change. We can think from scratch and make something much more fitting to the need.
Micro Fulfilment
“We don’t just sell the MDR, but have a mindset of helping customers understand and adopt more efficient solutions to improve logistic processes and energy consumption. While the market adapts globally, it can sometimes be hard for well implanted companies that have inventory and engineers experienced on one technology, to adopt a new model.” With the trend moving towards smaller and more local micro fulfilment centres, Itoh Denki seems well-placed to capitalise of the growth of facilities where smaller, more nimble material handling is required.